Bose's proactive system used currents and algorithms to make cars much calmer over bumps
We were recently amazed by Porsche’s new Active Ride system, which nullified roll and pitch in a 2.4-tonne Panamera Turbo, even at track speeds.
Twenty years ago, we were similarly impressed by novel suspension from a source we’d never have expected: Bose.
In the Porsche system, each damper is actuated by a sensor-fed unit, inside which electric motors drive hydraulic pumps to lower or raise the wheel, thereby keeping the car’s body level at all times.
In the Bose system, above each wheel where you would normally find a coil spring and damper was a linear motor containing coils and a magnet.
With current applied, this would raise or lower the wheel as much as 20cm from the car’s body – more than 100 times a second if required. The current came from a power amplifier, in response to signals from a sensor-fed computer running Bose’s own algorithms. Like the Porsche system, then, this was proactive, not reactive.
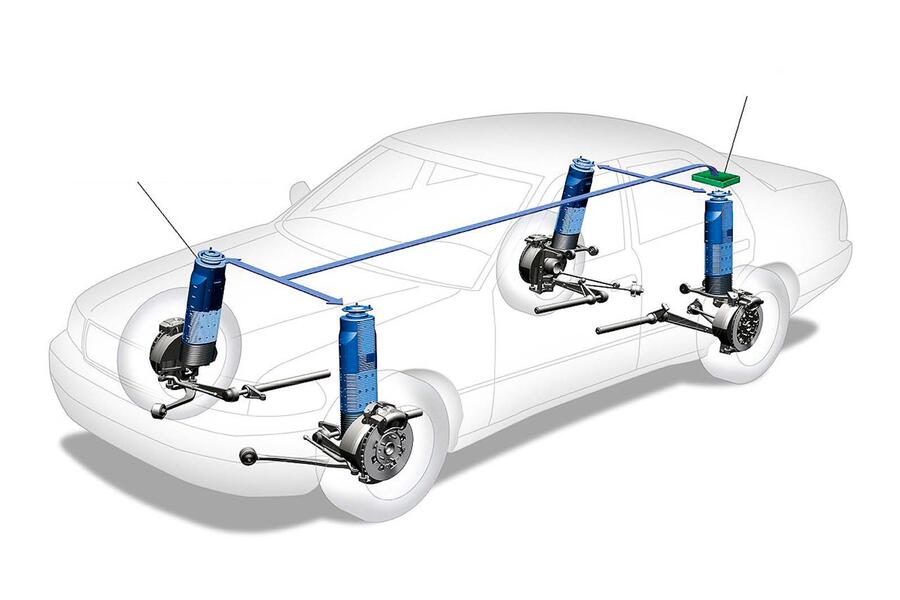
The car’s weight, meanwhile, was supported by torsion bars and MacPherson struts at the front and wishbones at the rear, and there was a damper inside each wheel to prevent excessive bouncing.
If any of this sounds familiar, it’s because the algorithm-controlled electromagnetic pulsing is how an audio speaker cone works, just on a much smaller scale, while the power amplifier uses switching methods from audio amplifiers.
The independent movement of the wheels prevented pitching and rolling – and even enabled the car to press into the ground and then literally jump over an obstacle! It could also have banked the car into turns, like some trains, but tests revealed the feeling made drivers do dangerous things.
Bose had fitted its system to a Mk2 Lexus LS. This is a limo that rides extremely smoothly anyway on its standard steel springs, so watch Bose’s demonstration here and you will be stunned by how great the improvement is over any surface.
The motors even did energy regeneration, whereas a shock absorber would just let energy go to waste, meaning the suspension system’s power use was only a third that of an air-conditioning system.

American Amar Bose earned a PhD in electrical engineering from the prestigious Massachusetts Institute of Technology (MIT) in 1956. He bought a premium stereo to celebrate but was disappointed by its sound quality, so he dived into researching audio science – which resulted in Bose launching his eponymous firm in 1964.
In these early years, he bought a Pontiac and a Citroën because he was interested respectively in their novel air springs and hydropneumatic spheres.
They inspired him to begin calculating the optimum suspension type in 1980, and his conclusion was that no conventional system had the speed, strength or efficiency to provide the contradictory qualities of ride comfort and body control – but an electromagnetic one might.
So a few engineers were tasked with improving linear electromagnetic motors, power amplifiers and control algorithms while correctly expecting a major increase in computing power. And as we have seen, it took a quarter of a century for their suspension to be ready for demonstration.
Bose wanted a luxury car firm to co-develop it. “It’s going to take some courage on [their] part,†he told us in 2004.
“We want someone whose philosophy is close to ours. We don’t want to cut corners that take the edge off. This could be more important than sound systems to Bose.â€
There were problems, though: Bose’s targeted extra weight was 90kg and the customer purchase cost was predicted by some to be as much as $10,000. Therefore no maker had that courage.
At least the tech was used to create active seats for truckers with bad backs – 97% of whom reported a significant comfort improvement. And then in 2017, four years after its founder died, Bose sold the tech to a firm created by ex-MIT students, Clearmotion, which recently announced that its CM1 ‘digital chassis’ would make its debut on the Nio ET9 electric crossover.
It isn’t electromagnetic but it is proactive, using Bose’s maths to control hydraulic units.