EV will use new production process and next-gen battery tech; brand claims 700 million in sales for car's lifetime
Tesla’s long-awaited entry-level electric car is finally set to enter production next year, giving the firm a foothold in the increasingly competitive sub-£25k sector.
The ‘Model 2’, as it is known, has been on the cards for years. Tesla CEO Elon Musk confirmed development was under way as long ago as 2020, but it was not until late last year that the first details began to trickle out and the firm announced plans to start building it in 2025.
Being developed under the codename ‘Project Redwood’, the secretive new model has a crucial role to play in helping Tesla defend its hard-won position among the world’s leading electric car manufacturers, having been knocked off the top spot in the final quarter of 2023 by BYD.
In fact, giving shareholders a forecast for the performance of its future product portfolio last year, Tesla boldly claimed that it could sell an astonishing 700 million Model 2s over its lifetime.
For context, the world’s best-selling car, the Toyota Corolla, has sold just over 50 million units since its introduction 58 years ago.
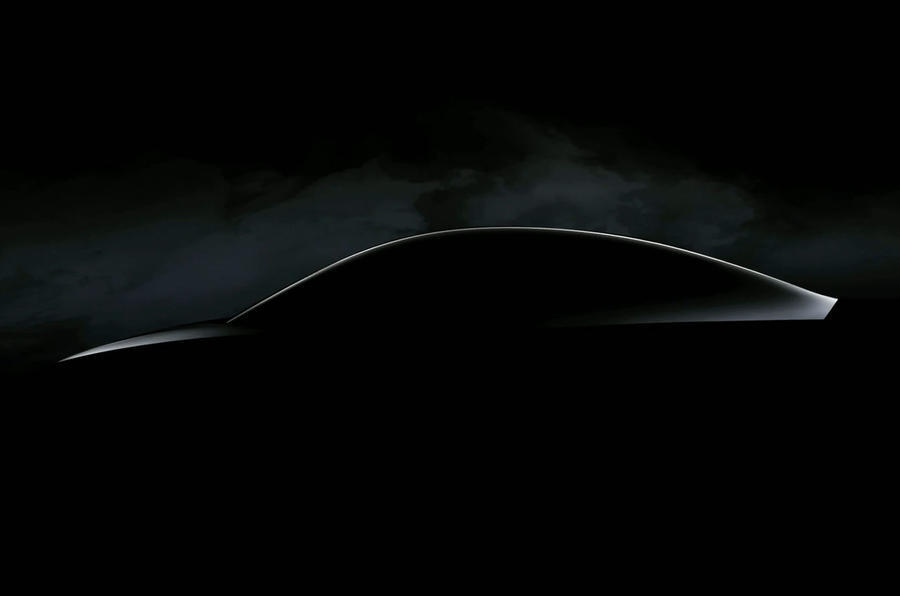
Nevertheless, the Model 2’s arrival will shake up a segment of affordability-focused compact electric family cars that is expanding in number and diversity as manufacturers take advantage of reduced EV production costs and seek to drive EV uptake with cheaper models.
Crucial to the Tesla’s viability in this context is a radical new production process that, the firm says, could save as much as 50% in build costs and speed up production times.
The ‘Unboxed’ process essentially revolves around reducing the amount of work done at each stage of the production line, avoiding any unnecessary movement or disassembly of the car or its components during its journey down the production line.
For example, the seats will be mounted directly to the underfloor battery pack, with the entire unit then raised into a bodyshell that has been painted in sections to avoid the need for door removal and reinstallation.
Next-generation powertrain and battery technology will be crucial to keeping costs down too. Tesla touts a 75% reduction in silicon carbide for its next batteries and the eradication of rare-earth metals in its new motors.
No powertrain details have been revealed for the Model 2, but it is likely to follow Tesla’s other models and be offered in single- and twin-motor forms, with the potential for high-performance versions to be introduced later on.

The Model 2’s platform is thought to be unrelated to that which underpins the larger Model 3 and Model Y, but it will be built using the same ultra-efficient gigacasting method, which breaks the structure into separate cast units in an effort to minimise the number of individual components and thereby its cost.
Initial production has been tipped for Tesla’s German factory near Berlin, a decision potentially made on the grounds that any smaller new model would be inherently geared towards the European market. Avoiding the cost of importing it from Tesla’s sites in Texas, Mexico or Shanghai will be another factor.
Musk has not been firm on a launch timeline for the new car but recently said he is “optimistic†about building the first car late next year.
Tesla is said to already be in conversations with parts suppliers for the new car and has acknowledged that its volume growth is expected to slow this year “as our teams work on the launch of the next-generation vehicleâ€.
The Model 2 is understood to be Tesla’s primary engineering focus and commercially it is much more important – and urgent – than the likes of the Roadster and Cybertruck.